What is the 'needle punch' process?
- dkfiber2004
- Nov 19, 2024
- 3 min read
Needle Punch is a nonwoven fabric manufacturing method where fibers are physically bonded together by puncturing them with needles.
This process forms a strong fabric through the entanglement of fibers, which is often used in various industries to create durable and versatile materials. Here's a breakdown of how Needle Punch works and its applications:
How Needle Punch Works
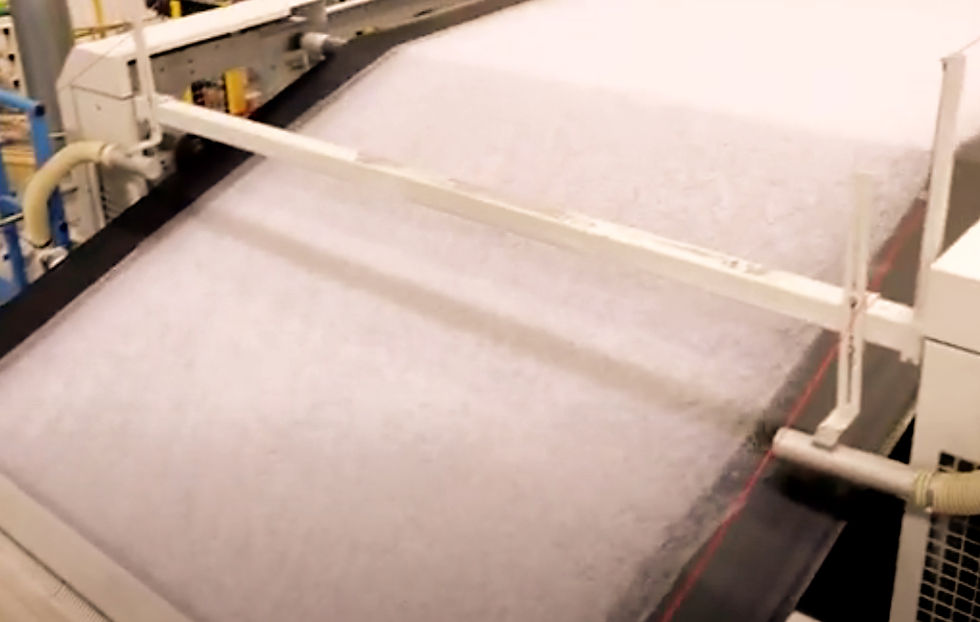
Fiber Layering: First, fibers are layered on a surface. These fibers can be made from materials such as polyester, nylon, or wool. in DK FIBER has 3D fibers specialized in needle punch process. (Show 3D polyester fiber)
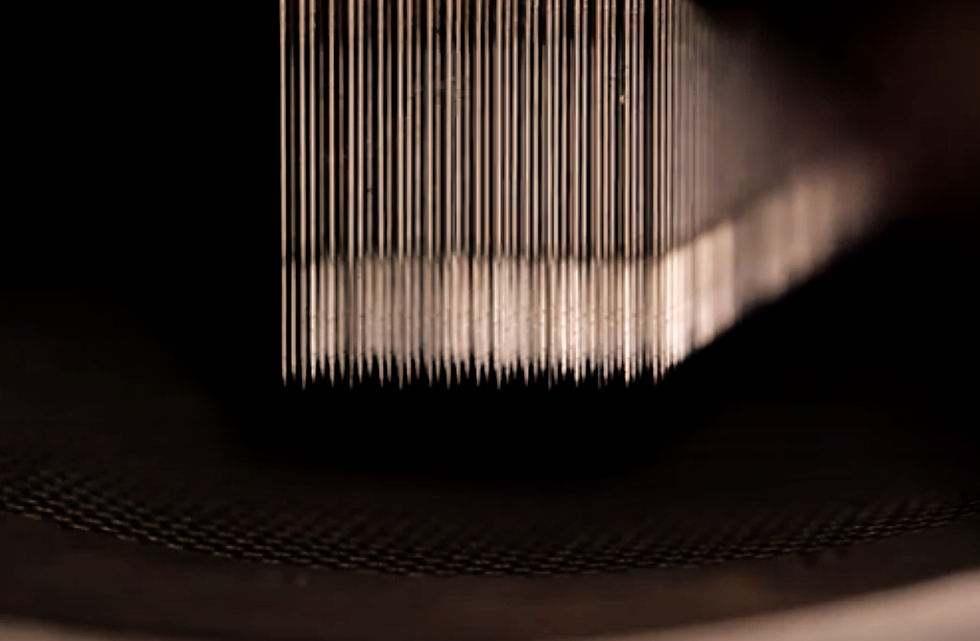
Needle Punching: A Needle Punch machine uses multiple needles that move rapidly up and down. The needles penetrate the fibers and physically entangle them, causing the fibers to bond together in a nonwoven pattern.

Fiber Bonding: As the needles puncture the fiber layers, the fibers get entangled and interlocked, creating a cohesive nonwoven fabric. The repetitive motion of the needles creates a strong fabric structure.
Post-Processing: After the fibers are bonded, the fabric may undergo heat treatment, compression, or other finishing processes to adjust its thickness, density, and strength.
Characteristics of Needle Punch
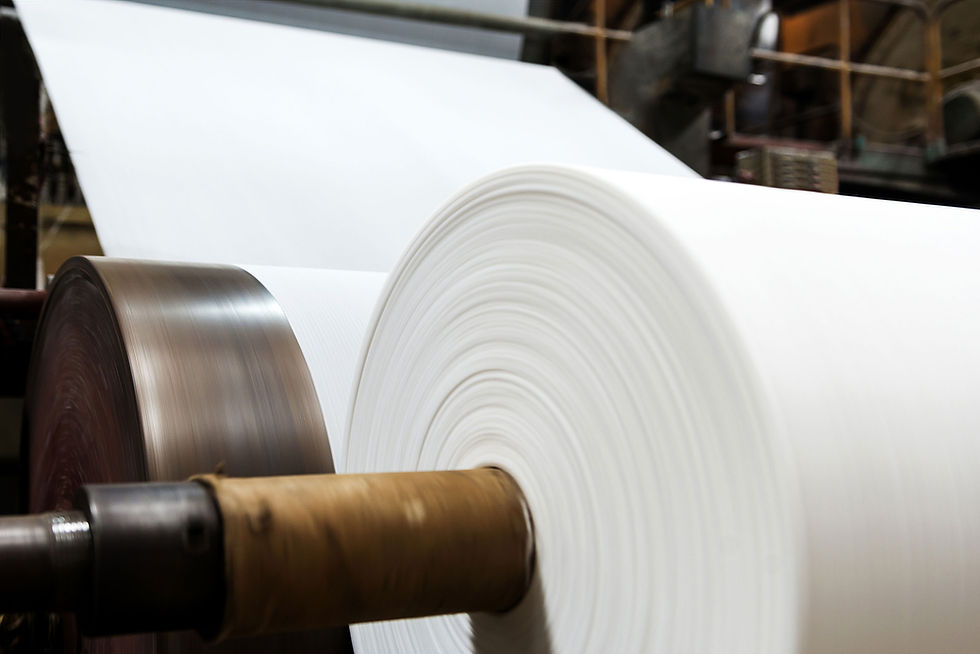
Durable and Strong: The fibers are interlocked firmly, making the fabric resistant to wear and tear. Needle-punched fabrics are known for their high durability and are resistant to abrasion.
Versatile: Needle-punched fabrics can be made in various thicknesses and densities, making them suitable for a wide range of uses such as padding, automotive seating, filters, blankets, and upholstery.
Flexibility: These fabrics are soft and flexible while still maintaining their strength and durability.
Eco-friendly: Needle punching is a physical bonding process, meaning it doesn't require the use of chemicals or adhesives, making it more environmentally friendly compared to other methods.
Applications of Needle Punch Fabrics

Automotive Industry
Used in seat covers, headliners, and other interior components due to its high durability and ability to absorb shock.

Bedding and Furniture
Used as filling material in comfort products like quilts, pillows, and mattresses, providing cushioning and softness. Also used in upholstery and other furniture items.
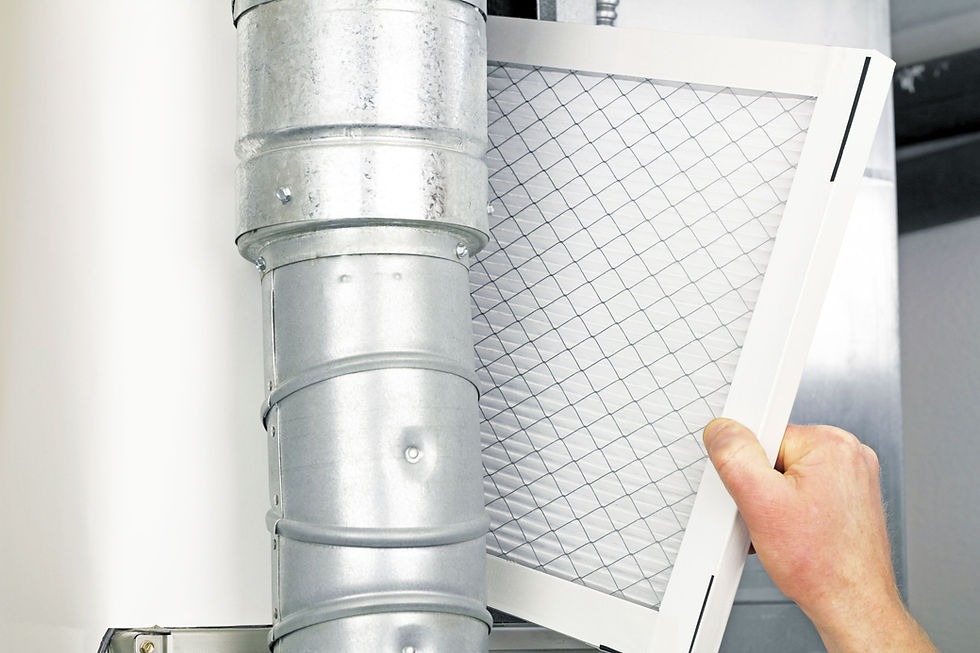
Filtration Materials
Needle-punched fabrics are commonly used in the production of nonwoven filter media for air, water, and liquid filtration. Their consistent density and strength make them ideal for filtering applications.

Industrial Fabrics
Used in safety products, workwear, and insulation materials. The fabric's ability to absorb shock and sound makes it useful for noise reduction and impact protection.
Advantages and Disadvantages of Needle Punch

Advantages
High Durability: The fibers are physically entangled, making the fabric highly durable and resistant to wear, tear, and abrasion.
Customizable Design: Needle punching allows for flexibility in creating fabrics with varying thicknesses and densities, making it suitable for a wide range of applications.
Eco-friendly: Since the bonding is done without the use of chemicals or adhesives, the process is more environmentally friendly compared to other methods.
Disadvantages
Cost: The machinery and production line for Needle Punching can be expensive, and small scale production may result in higher costs.
Precision: While Needle Punching can create strong fabrics, achieving precise patterns or designs can be challenging. The uniformity of thickness and density may also be difficult to control in some cases.
Needle Punch is a process used to create strong and durable nonwoven fabrics by physically entangling fibers using needles.
This process results in fabrics that are widely used in industries such as automotive, bedding, furniture, filtration, and industrial applications.
The fabric produced through Needle Punching is highly durable, flexible, and eco-friendly, making it a preferred choice for many applications.